CNC Machining ABS Insulation Boards: A Perfect Blend of Efficiency and Precision.
CNC machining ABS insulation boards is all about efficiency and precision—a match made in heaven. As a versatile insulation material, ABS boasts moderate hardness, making it easy to cut with CNC tools. Whether it's straight cuts, grooves, or intricate patterns, insulation material CNC processing delivers quick, high-quality results. The dimensional accuracy is spot-on, with tolerances controllable down to decimal places, ensuring insulation material CNC machined parts meet strict specifications.
From prototyping to mass production, insulation material processing via CNC ensures consistency and reliability, making it a worry-free choice for custom parts or functional models.

Key Considerations for CNC Machining ABS Boards:
1.Watch the Heat
ABS isn’t heat-resistant, so avoid excessive spindle speeds (6,000–8,000 RPM is ideal) and keep feed rates moderate. Otherwise, the surface may melt into a "chocolate sauce" mess, and edges can warp or deform.
2.Secure Clamping
ABS is relatively soft, so avoid over-tightening clamps to prevent marks—but don’t leave it loose either, or the board may slip during cutting. Use soft padding or adjust clamping pressure for a balanced hold.
3.Choose the Right Tool
Don’t force metal-cutting tools on ABS! Opt for coated end mills or tungsten carbide tools with sharp edges. Replace dull blades promptly to avoid melted chips sticking to the tool and ruining the finish.
4.Clear Chips Promptly
ABS chips are lightweight and can clog tool paths. Use coolant or an air blast during machining to keep chips from piling up, ensuring a smooth surface.
5.Leave Allowance
While CNC is precise, ABS may shrink slightly after cooling. Add an extra 0.1–0.2mm to dimensions in your design to allow for post-machining adjustments or polishing.
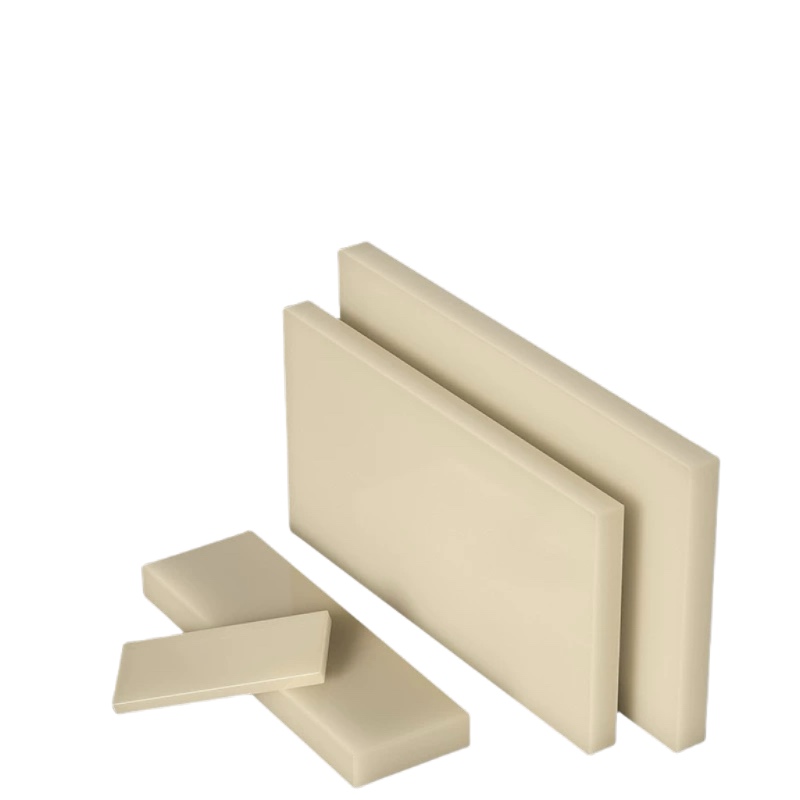