Aluminum material skived fin heat pipe heat sink for 3000W laser cooling system1
3 year ago
To design a skived fin heat pipe heat sink for a power dissipation of 3000W, several factors need to be considered, Die Casting such as the heat pipe size, number of fins, and material selection. Here is a general approach to designing such a heat sink:1. Determine the heat pipe size: The heat pipe should be selected based on the required thermal conductivity and heat transfer capacity. A larger heat pipe diameter will generally have a higher heat transfer capacity. Common heat pipe diameters range from 4mm to 10mm. For a high power dissipation of 3000W, a larger diameter heat pipe, such as 8mm or 10mm, would be suitable.2. Calculate the number of heat pipes: The number of heat pipes required depends on the power dissipation and the heat pipe's individual heat transfer capacity. For example, if a single heat pipe can handle 500W, Pressure Die Casting six heat pipes would be needed for a total power dissipation of 3000W.3. Determine the heat sink size: The heat sink size should be chosen based on the available space and the desired thermal performance. The larger the heat sink, the more surface area available for heat dissipation. It is essential to ensure that the heat sink can accommodate the required number of heat pipes.4. Determine the fin density: The fin density affects the heat dissipation capability of the heat sink. Higher fin density provides more surface area for heat transfer but may increase air pressure drop. The fin density should be optimized based on the available space and desired thermal performance.5. Select the material: The material choice for the heat sink should consider its thermal conductivity, weight, and cost. Aluminum is a common material choice due to its good thermal conductivity, lightweight, and cost-effectiveness. However, for higher thermal conductivity requirements, copper or copper alloys can be considered.6. Design the fin shape: The shape and dimensions of the fins will impact the overall thermal performance. The fin shape can be optimized to enhance heat transfer and minimize air pressure drop. Common fin shapes include straight fins, pin fins, and louvered fins.7. Consider additional features: Depending on the application, Bonded Fin Heat Sink additional features such as heat pipes with embedded wick structures, heat spreaders, or heat pipes with vapor chambers can be incorporated to enhance heat transfer performance.It is important to note that the specific design parameters will depend on the specific requirements of the application, and detailed calculations and simulations should be carried out to optimize the design. Consulting with a thermal engineer or utilizing specialized heat sink design software can be beneficial in achieving the desired thermal performance.
Product Description
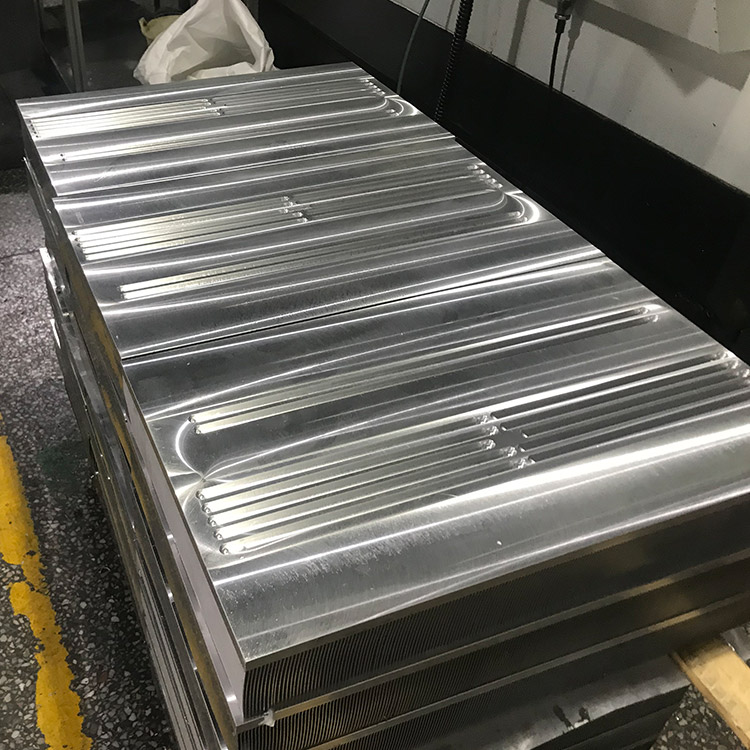
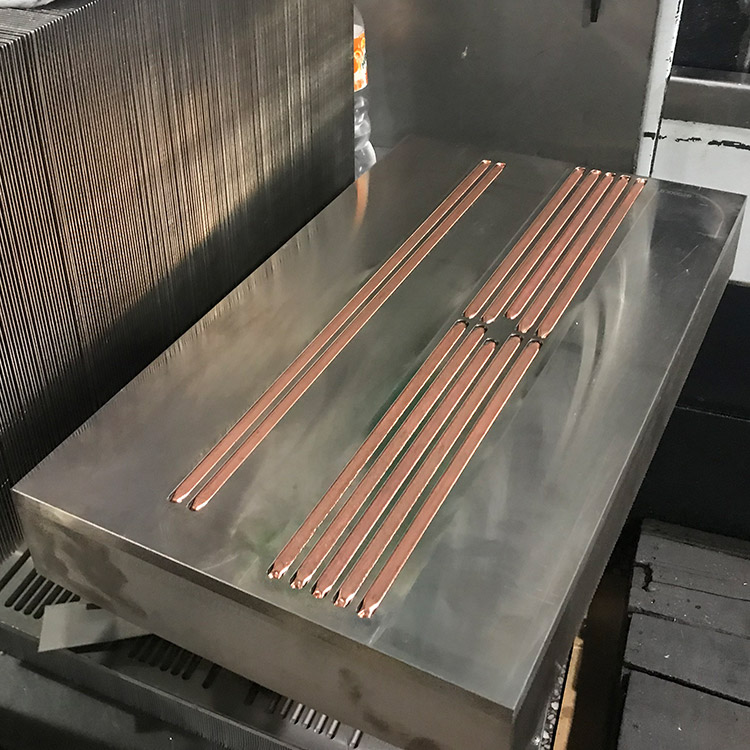
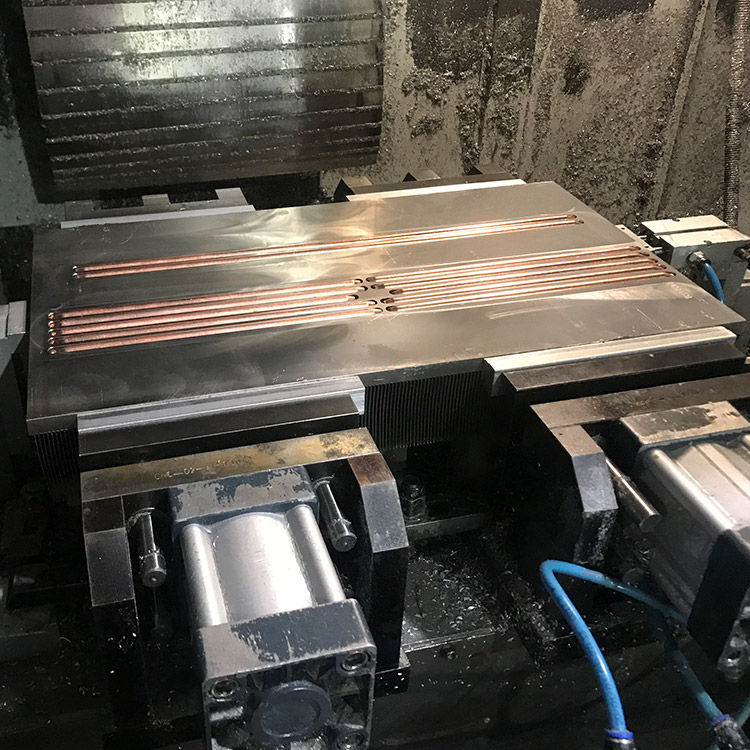
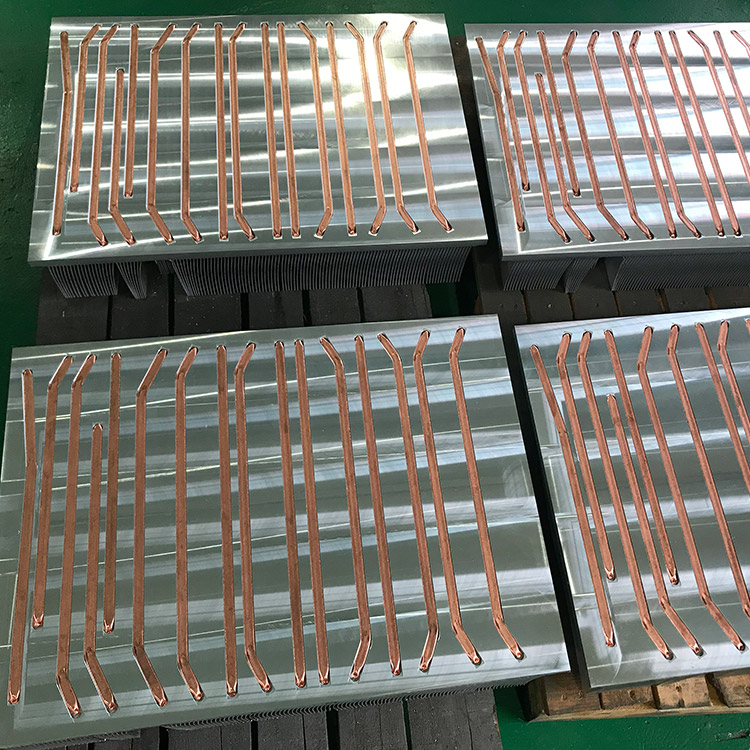
Product name
|
CPU Server AMD AM5 1U1CA
|
Making process
|
Soldering process+copper plate+al fin+heat pipe
|
Size
|
78mm*104mm*24.5mm
|
Material
|
Copper plate+al fin+heat pipe
|
Similar Video Recommendation
You May Also Like
If you are interested in the product, contact Bossgoovideo.com for more information
- *To:
- Suzhou Wint Electric Co., Ltd
- *Message:
-
Submit
Main Product:
Liquid Cold Plate ,
Friction Stir Welding Heatsink,
Tubed Liquid cold plate,
CPU Server,
Bonded Fin Heat Sink,
Heat Pipe Heat Sink