CNC workshop processing mold
9 month ago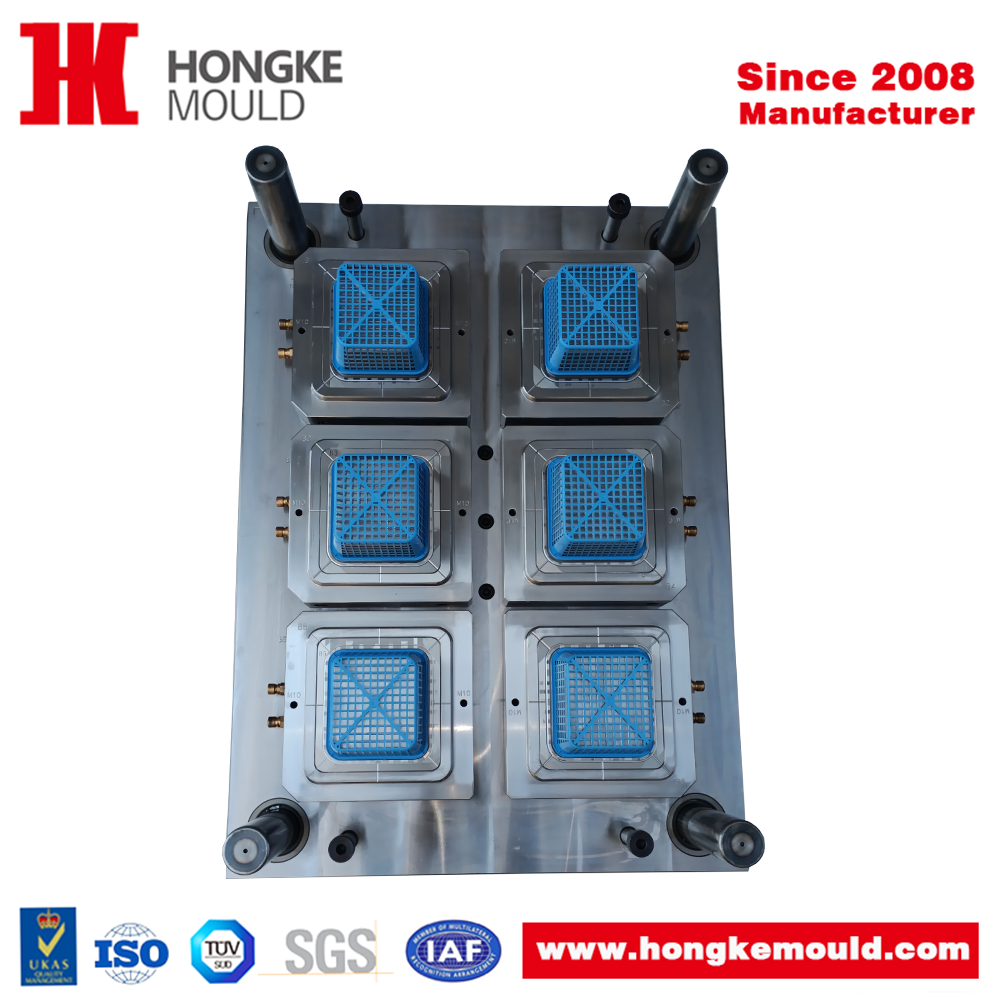
Precision · Reliability · Efficiency – Hongke Hot Runner Molds Redefine PP Basket Manufacturing Excellence
In the competitive plastics industry, production efficiency, mold longevity, and product consistency determine market leadership. As a technology-driven mold manufacturer with decades of expertise, Hongke presents our 6-cavity Hot Runner Injection Mold for PP Baskets – engineered for 500,000+ cycles durability, 3μm precision verification, and full-process quality control, delivering turnkey manufacturing solutions from precision mold making such as Car Moulds For Auto Structural Component,Medical Plastic Molds to injection molding.
I. Engineering Excellence: Technology-Driven Productivity
1. Material & Structural Optimization
Our PP basket-specific mold combines S136 hardened cavity steel with SKD11 hardened core steel, achieving exceptional wear resistance and corrosion protection to withstand repeated high-pressure PP injections. The S50C mold base ensures structural integrity, while the integrated Yudo Hot Runner System enables precise temperature control and zero material waste, reducing cycle times by 10%-20%.
2. 6-Cavity Design for Scalable Output
Multi-cavity synchronization technology breaks traditional productivity limits, yielding 6 finished products per injection cycle. Combined with our 30T-450T injection molding machines, we support flexible production scaling from prototyping to high-volume orders.
II. Quality Assurance: Globally Certified Standards
1. Precision Beyond Industry Norms
Our FAI, CPK, IQC/IPQC/OQC inspection protocol maintains ±0.03mm critical dimension tolerance. The 3μm-resolution CMM conducts full-dimensional scans on molds and products, eliminating batch defects.
2. Internationally Recognized Certifications
Compliant with ISO9001:2015, IATF 16949:2016, ISO 14001:2015 & ISO13485:2016, we serve automotive, medical, and consumer, electronics customers while meeting EU RoHS/REACH requirements for global market access.
3. 500,000-Cycle Lifetime Guarantee
Leveraging 17+ years in complex mold design, we optimize cooling systems and ejection mechanisms through mold flow simulation. Combined with specialized heat treatment for H13/SKD11 steels, our molds deliver minimum 500,000 cycles, reducing per-unit costs by 22-35%.
III. Reasons to Choose Hongke: From Manufacturing to Value Creation
-
Expert Engineering Team
17+ years experienced designers holding several patents, specializing in PP basket challenges: deep-cavity demolding, thin-wall distortion prevention. -
Proven Production Capacity
400-500 molds/year output with monitored schedules, maintaining 98%+ on-time delivery rate. -
Low-Risk Pilot Production
Free trial molding & small-batch runs ensure performance validation before shipment. -
Cost-Efficient Solutions
Mold flow analysis prevents design flaws, reduces trial attempts and cuts total costs by 10-20% vs industry averages. -
Seamless Global Collaboration
Bilingual project teams offer support with DFM reports, T0/T1/T2/T3 trial reports and videos, and weekly mold status reports.
Submit your product drawings to receive DFM analysis & quotation within 48 hours.
Similar Video Recommendation
You May Also Like
If you are interested in the product, contact Bossgoovideo.com for more information
- *To:
- Dongguan Hongke Plastic Precision Mould Co.,Limited
- *Message:
-
Submit
Main Product:
mold making,
injection molding,
injection mould,
plastic injection mold,
plastic molds ,
plastic making